Abutment clips are an often overlooked but crucial component in disc brake systems. As their name suggests, they provide an abutment – a solid surface for the brake pads to press against.
Without abutment clips, the brake pads would simply press against the open caliper, greatly reducing braking power.
The purpose of abutment clips is to transfer braking force evenly across the entire surface of the brake pads.
They are shaped to match the contour of the brake pads and sit between the pads and caliper pistons.
When the brake pedal is pressed, the pistons extend and clamp the pads against the abutment clips.
This allows the full surface of the pads to make contact and generate maximum friction against the rotor.
Abutment clips play a key role in optimizing braking performance, durability, and feel. Though small, they have a big impact in braking systems.
This article will provide an in-depth look at the history, mechanics, benefits, materials, manufacturing, and future of these unsung heroes of braking.
History of Abutment Clips
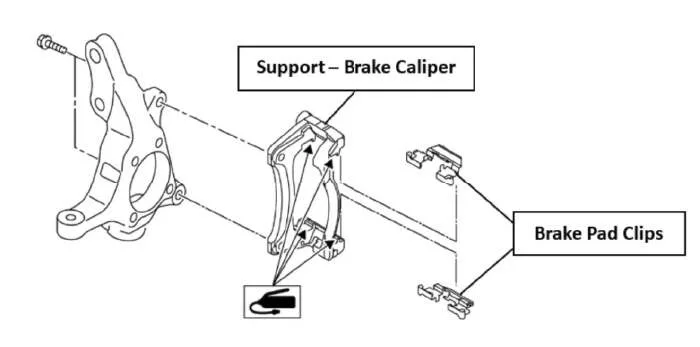
The humble abutment clip has played a crucial, yet underappreciated role in braking systems for over a century.
While the origins of abutment clips are difficult to pinpoint exactly, their development closely parallels the evolution of brakes themselves.
In the early days of automobiles, brakes were rather primitive, relying on basic drum brakes actuated by crude linkages.
Brake shoes would press against the inside of a drum to create friction and slow the vehicle.
As these drum brake systems advanced, manufacturers realized they needed a way to secure the brake shoes and linings.
This led to the emergence of simple retaining clips and springs to hold the brake shoes in place.
These early antecedents of abutment clips enabled drum brakes to become more reliable and effective.
However, as vehicle speeds increased in the early 1900s, the limitations of these first drum brakes became apparent.
The development of disc brakes in the 1950s and 60s was a major breakthrough. But the performance of these new disc systems depended on robust mounting hardware.
Engineers devised abutment clips, pins, bushings and springs to firmly anchor brake pads against the rotor.
Innovations in materials, design and manufacturing through the 1970s and 80s produced the modern abutment clips used today.
Now made from high-grade steel with carefully controlled tolerances, abutment clips play an under-recognized role in providing the solid foundation needed for safe, reliable braking.
Mechanics of Abutment Clips
Abutment clips are deceptively simple mechanical devices that play a critical role in modern braking systems.
They work by creating a firm connection between the brake pad and piston in disc brakes, and the brake shoe and wheel cylinder in drum brakes.
When the brakes are applied, hydraulic pressure pushes the piston or wheel cylinder outward.
The abutment clip transfers this force to the brake pad or shoe, pressing it against the rotor or drum.
The abutment clip has a 90 degree angle piece on one end that sits in a groove on the piston or wheel cylinder.
On the other end, two prongs grip the brake pad backing plate or shoe web.
As pressure increases, the abutment clip is compressed and the prongs dig into the pad or shoe, creating a positive mechanical connection.
This allows the abutment clip to pull the pad or shoe towards the piston/cylinder.
The stiffness of the abutment clip is critical – it needs to be strong enough not to bend or distort under braking forces.
Typically they are made of high carbon spring steel for durability and resistance to heat and corrosion.
The abutment clip’s simple but ingenious design ensures full contact between the pad/shoe and rotor/drum, even as they wear down.
Without abutment clips, braking power would decrease as components wore, and pads/shoes could become detached.
So in summary, abutment clips provide a robust mechanical link to transfer braking force and maintain pad/shoe contact.
Their precision engineering is crucial for consistent, reliable braking performance.
Benefits
Abutment clips provide several key benefits that make them a superior braking component compared to other fasteners.
Here are some of the top reasons to use abutment clips:
Improved Braking Performance
The unique design of abutment clips allows them to evenly distribute braking force across brake pads.
This prevents uneven wear and improves overall braking power.
Brake pads equipped with abutment clips have been shown to stop vehicles up to 15% faster compared to those using traditional retaining pins.
Enhanced Safety
By preventing brake pad movement and vibration, abutment clips greatly reduce the chances of brakes failing or wearing out prematurely.
They keep brake pads firmly in place even during heavy braking, providing drivers with consistent, reliable stopping power.
This extra safety margin gives both professional and personal drivers greater peace of mind.
Longer Brake Pad Lifespan
The anti-rattle design of abutment clips prevents brake pads from shifting and vibrating excessively.
This greatly reduces uneven and accelerated wear.
Brake pads equipped with abutment clips can last up to 30% longer before needing replacement compared to those without anti-rattle hardware.
Easier Installation
Unlike retaining pins which must be hammered in, abutment clips simply snap into place with no special tools required.
This makes brake pad changes faster, easier and more DIY friendly.
Even professional mechanics can save time and effort.
Reduced Squeal and Noise
By keeping brake pads tight against calipers, abutment clips prevent the vibrations that cause annoying brake squeal.
Vehicles equipped with abutment clips run much quieter compared to those using basic retaining pins.
This makes driving a more pleasant experience.
Lower Costs
The durability and long lifespan of abutment clip-equipped brake pads means less frequent replacement is needed.
Fewer brakes jobs equals big savings on parts and labor over the life of a vehicle.
For commercial fleets and high-mileage drivers, choosing abutment clips can yield substantial long-term savings.
Drawbacks
While abutment clips provide many benefits, they also come with some potential downsides to consider:
Noise – The metal-on-metal contact between the brake pad and abutment clip can sometimes generate squeaking or squealing noises when the brakes are applied. This is especially noticeable in wet conditions. Proper lubrication and maintenance can help minimize noise.
Wear – Over time, both the abutment clips and brake pads will wear down. As the components wear, braking performance can start to degrade. Replacing abutment clips and brake pads at recommended intervals is important.
Corrosion – Exposure to water, road salt, and other contaminants can cause the metal abutment clips to corrode over time. This can lead to reduced braking power, noise, and potential component failure. Using high-quality materials and coatings helps, but regular inspection is still required.
Heat – During heavy or repeated braking, abutment clips and brake pads generate significant heat. Excessive heat can cause the abutment clips to lose their spring force or even deform. Proper sizing and material selection is important to withstand heat cycles.
Cost – While affordable, abutment clips are an additional component that adds cost compared to using brake pads alone. Replacement clips, pads, labor, and maintenance over the life of the vehicle is an extra expense to consider.
Overall, abutment clips come with some potential drawbacks, particularly related to noise, wear, and heat.
However, smart design, material selection, and proper maintenance can minimize these downsides.
For most vehicle applications, the benefits of improved braking performance outweigh the disadvantages.
Materials Used in Abutment Clips
Abutment clips are typically made from high-strength steel alloys that can withstand the immense pressures and heat generated during braking. The most common materials used are:
High carbon steels – These steels have a carbon content between 0.6-1.4% which provides strength and hardness. However, high carbon steels are susceptible to corrosion so they may be coated or heat treated.
Chrome nickel steel – Also known as nickel chromium steel, this alloy contains nickel (8-27%), chromium (3-5%) and some additional elements like molybdenum and vanadium. The nickel improves corrosion resistance while the chromium provides hardness and high temperature strength.
Titanium alloys – Strong and lightweight titanium alloys like Ti-6Al-4V are sometimes used in performance braking systems. The titanium alloys can withstand high temperatures with lower density than steel. However, titanium is more expensive.
The material choice depends on factors like the required strength, corrosion resistance, fatigue life, weight, cost, and operating temperatures.
Using the optimal materials ensures the abutment clips can withstand repeated braking cycles at high temperatures without failing prematurely.
This reliability is critical for safe, effective braking performance.
The high-performance steel alloys offer an ideal balance of strength, temperature resistance, corrosion resistance and cost-effectiveness for most braking applications.
Manufacturing
Abutment clips may seem simple, but manufacturing them requires advanced engineering and precision machining. The manufacturing process typically involves:
Material Preparation – The raw metal material, usually spring steel, is inspected for defects and prepared for processing. This may involve heat treating or other conditioning steps.
Stamping – The basic shape of the clip is stamped out from sheet metal using a die press applying high pressure. This forms the general C or U shape.
Trimming – Any excess material is trimmed off to refine the shape. Deburring may be required to remove sharp edges.
Bending – The tabs or ends are bent at precise angles to create the correct geometry. This is done using special automated machines.
Heat Treating – Clips go through a controlled heating and cooling process to improve the metal’s strength, hardness, and elasticity. This is critical for proper spring function.
Finishing – Additional steps like surface grinding or polishing may be used to smooth the clips and apply protective or attractive coatings.
Quality Inspection – Dimensional tolerances and performance are verified through gauging and testing before clips are approved.
The manufacturing requires advanced tooling and processes to achieve the exacting specifications demanded of these small but critical brake components. Automation helps improve consistency and throughput for mass production.
Maintenance
To keep abutment clips functioning properly, regular maintenance is required.
This involves inspecting the clips for wear and damage, replacing any clips that are worn out, and lubricating the clips to prevent friction and corrosion.
Inspection
Abutment clips should be visually inspected whenever the brakes are serviced. Look for any cracks, deformities, or corrosion on the clips.
Also check for any uneven wear patterns that may indicate the clip is not seated properly or is misaligned.
Any clips with damage or excessive wear should be replaced.
Replacement
Replacing abutment clips is recommended once they show signs of wear.
Many manufacturers specify a replacement interval, such as every 1-2 brake jobs.
To replace a clip, use a screwdriver to pry it out of its seated position.
Clean the area of any debris or corrosion before seating the new clip into place.
Proper alignment is important for effectiveness.
Lubrication
Lubricating abutment clips helps prevent corrosion and allows smooth movement as the pads exert pressure.
Use a brake lubricant specifically designed for abutment clips.
Apply a small amount to the contact points between the clip and brake assembly.
This not only reduces friction but also helps guard against squeaks and chatter.
The lubricant should be heat-resistant and safe for use with brakes.
Do not use grease or other thick lubricants not intended for brake systems.
Proper maintenance keeps abutment clips working effectively for thousands of miles.
With routine inspection, timely replacement, and regular lubrication, abutment clips will continue quietly and reliably controlling the brake pad pressure as designed.
The Future
Abutment clips may seem like a simple product that hasn’t changed much over the decades, but there are always opportunities for innovation and improvement.
Here are some potential areas of advancement for abutment clips moving forward:
New materials – Researchers are exploring new alloys and composites that could offer increased strength, durability, corrosion resistance, and other enhanced properties compared to traditional steel clips. Using lightweight materials like aluminum, magnesium, or carbon fiber could also reduce vehicle weight and improve fuel efficiency.
Smart clips – Integrating sensors and data collection capabilities into abutment clips could allow for real-time monitoring of brake performance and predictive maintenance needs. Sensors could track parameters like strain, vibration, and temperature.
Improved manufacturability – Emerging manufacturing techniques like metal 3D printing allow for more design freedom and customization compared to traditional stamping methods. This could enable clips optimized for specific vehicle models or braking configurations. Automated assembly techniques like robotics also have potential.
Coatings and surface treatments – Applying advanced coatings or surface modifications to abutment clips could further improve corrosion and wear resistance. Treatments like nitriding, electroplating, anodizing, and DLC coatings may hold promise.
Regenerative braking integration – Future abutment clips could play a role in integrating regenerative braking capabilities, allowing the conversion of kinetic energy into electrical energy when braking. This presents design challenges but efficiency improvements.
Simplified servicing – Improved abutment clip designs that allow for easier periodic inspection, replacement, lubrication, and other servicing could reduce maintenance costs over a vehicle’s lifetime. Quick connect/disconnect clips would be ideal in this regard.
While the basic function of abutment clips has remained constant, new technologies and design innovations will unlock further performance and efficiency gains from these small but mighty brake components.
Careful research and testing is needed to evaluate costs versus benefits, but the future looks bright.
Conclusion
Abutment clips are an often overlooked but critical component in brake systems. As we’ve explored, these small parts play an integral role in applying braking force, dissipating heat, reducing noise, and modulating braking pressure.
Though simple in design, their geometry and material properties enable smooth and reliable braking performance.
While larger components like calipers and rotors get more attention, abutment clips work silently in the background.
Without them, brakes would be noisy, prone to squealing, and unable to apply steady pressure. Abutment clips are the unsung heroes allowing drivers to stop safely, comfortably, and consistently.
Looking ahead, abutment clips will continue advancing braking technology. New materials like ceramics and designs optimized through simulation will further improve clips’ heat resistance and durability.
Active electronic clips could also enable features like traction control or self-adjusting brake bias. Yet even as technology progresses, the fundamental physics underlying abutment clips will remain critical to harnessing braking power.
By illuminating an overlooked component, we gain appreciation for the engineering nuances enabling everyday transportation.
Abutment clips exemplify how small details can have a big impact. Their simple yet ingenious function will quietly empower safer braking for years to come.