A torque wrench is a vital tool used to tighten bolts and fasteners to a specific torque value.
Proper torque application is extremely important when working with mechanical assemblies to ensure parts are fastened securely without causing damage.
Applying too much torque can overtighten the fastener, leading to stripping or breakage.
Not enough torque results in a loose assembly that can fail or leak.
Using a torque wrench allows precise control over the amount of rotational force, measured in torque units like Newton-meters or foot-pounds, delivered when tightening a fastener.
This ensures each fastener receives the exact torque specified by the manufacturer to create a tight seal or hold components together without complications.
By using the proper torque value, mechanics can avoid costly mistakes like warped parts, leaks, or dangerous malfunctions.
The torque wrench gives technicians and do-it-yourselfers peace of mind that their critical fasteners are tightened to the right specifications for optimal performance and safety.
This guide will provide a comprehensive overview of how to properly use a torque wrench for any assembly task.
Types of Torque Wrenches
Torque wrenches come in a variety of styles, each with their own advantages and disadvantages. The main types are:
Beam Torque Wrenches
Beam torque wrenches are the simplest style.
They consist of a long beam with a torque measurement scale and a pointer that indicates the amount of torque being applied.
Pros:
- Simple, easy to use design
- Durable
- Relatively inexpensive
Cons:
- Require more skill to read the dial
- Not as accurate as other types
Click Torque Wrenches
Click torque wrenches make an audible “click” sound when the preset torque level is reached.
This signals to the user to stop applying torque.
Pros:
- Very accurate once properly set
- Don’t require watching a dial
- Easy for anyone to use
Cons:
- More expensive than beam types
- Prone to damage if over-torqued
Dial Torque Wrenches
Dial torque wrenches have an adjustable dial that indicates the amount of torque being applied.
Pros:
- Very precise torque settings
- Easy to read measurement dial
Cons:
- More expensive than beam types
- Dial is prone to damage if dropped
Digital Torque Wrenches
Digital torque wrenches have an electronic digital display and are the most advanced style.
Pros:
- Extremely accurate
- Digital display is easy to read
- Can store torque measurement data
Cons:
- Most expensive type
- Require batteries or charging
- Electronic components can fail
The choice comes down to the required precision, budget, and how often the wrench will be used.
For occasional use, a beam or click wrench is sufficient for most DIY mechanics.
Professional automotive use requires a high-end digital or dial wrench.
How Torque Wrenches Work
Torque wrenches are designed with an internal mechanism that allows them to precisely measure and indicate the amount of torque being applied to a fastener.
The core principle behind their operation is the relationship between torque and the twisting force applied along a lever arm.
Inside a torque wrench is a calibrated spring that is connected to the handle on one end and the head on the other.
As you pull on the handle when tightening a fastener, the spring twists and compresses.
The greater the force applied, the more the spring coils and builds tension.
The head contains a gearing system that translates this spring tension into a measurable torque value.
Most torque wrenches have a dial or digital readout that displays the real-time torque as you tighten.
When the preset torque value is reached, the internal mechanism triggers the wrench to “click” or make a sound to notify the user.
Higher quality torque wrenches use more sophisticated designs to ensure accuracy.
For example, some contain multiple springs or use a beam design consisting of levers and pivots.
Regardless of the exact engineering, all torque wrenches operate by converting the linear force from your hand into a rotational force (torque) that can be precisely measured and controlled.
By using mechanical principles like levers and springs, torque wrenches allow operators to reliably tighten fasteners to the correct degree without overtightening.
The preset torque value eliminates human guesswork and prevents damage caused by over- or under-tightening.
Selecting the Right Torque Wrench
Choosing the right torque wrench for the job is critical to ensure you apply the proper amount of torque without damaging the fasteners or components.
There are several factors to consider when selecting a torque wrench:
Required Torque Range
First, determine the range of torque values needed for your application.
Torque wrenches are available with different torque ranges based on the mechanism and size.
For automotive use, a common range is 10-150 ft-lbs.
Industrial applications may require up to 600 ft-lbs or more.
Choose a wrench that can reliably produce the minimum and maximum torque needed.
Using a wrench at the high end of its range will decrease accuracy.
Precision
The precision of the torque wrench determines thesmallest increment of torque it can measure.
Precision is usually given in percentages – common values are ±3%, ±4%, or ±5% of the torque reading.
Higher precision wrenches cost more but provide more accurate torque applications.
Drive Size
Torque wrenches come in different drive sizes – the most common being 1/4″, 3/8″, and 1/2″ square drives.
Choose a drive size that fits the fasteners you’ll be working with.
Using socket adapters can lead to inaccurate torque.
Ratchet or Straight Head
Decide if you need the mobility of a ratcheting wrench or the accessibility of a straight fixed-head wrench.
Ratcheting wrenches allow you to torque fasteners in tight spaces.
Straight wrenches provide the most accurate torque settings.
Price
In general, accuracy and durability increases with price.
For occasional use, an inexpensive general-purpose wrench may suffice.
For frequent industrial use, invest in a high-quality wrench to provide reliable precision and longevity.
Consider your specific torque needs and choose the simplest wrench that will get the job done accurately.
Using the right torque wrench helps ensure proper tightening while avoiding damage from overtightening.
Reading the Torque Scale
Torque wrenches have measurement scales that indicate how much torque force is being applied.
Understanding how to read these scales is important for using a torque wrench correctly.
The scale on a torque wrench is typically marked in increments of foot-pounds, inch-pounds, or Newton meters.
The units used will depend on the torque wrench type and its intended applications.
Beam Style Torque Wrenches
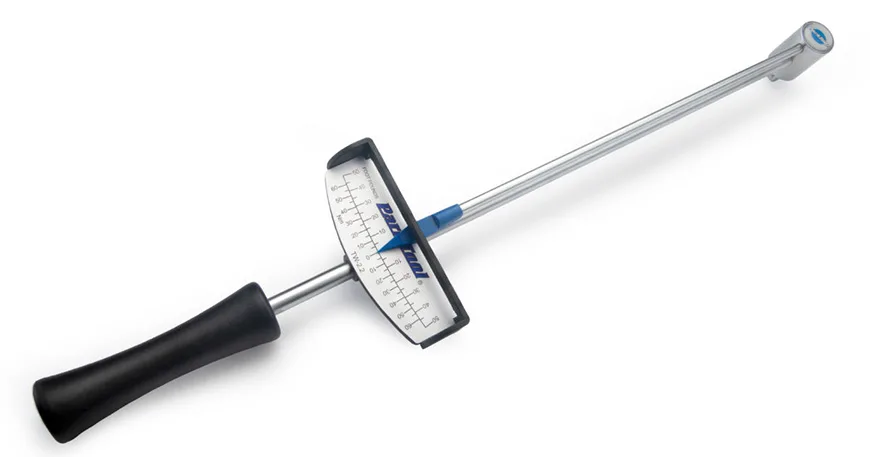
Reading the scale on a beam style torque wrench
Beam style torque wrenches have a long lever arm and a pointer that indicates the torque setting on a scale.
As you pull on the handle, the pointer will move and indicate the amount of torque being applied.
For example, a beam torque wrench may have a scale marked from 0 – 100 ft-lbs in increments of 5 ft-lbs.
If the pointer is sitting at the 60 ft-lbs mark, that indicates you are applying 60 ft-lbs of torque to the fastener.
The measurement scales on beam wrenches are typically accurate to within +/- 4% of the indicated value.
Dial/Digital Torque Wrenches
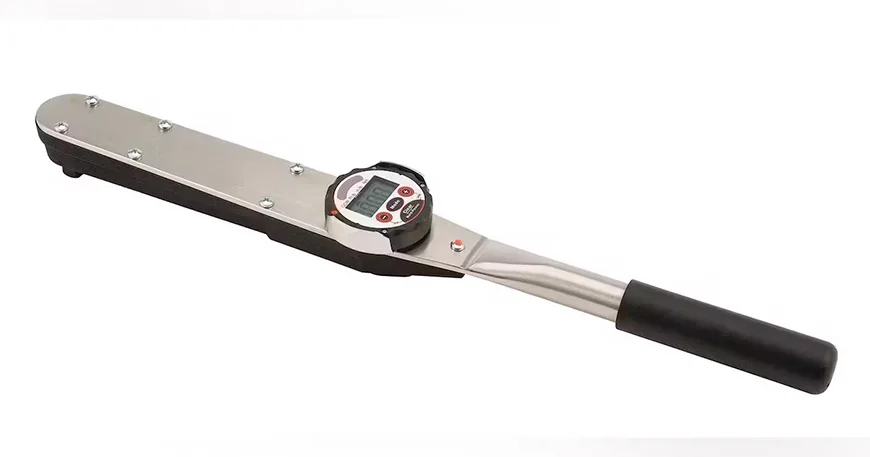
Reading the dial scale on an electronic torque wrench
Dial and digital torque wrenches have an electronic or mechanical dial that displays the real-time torque value as you tighten a fastener.
For example, a dial may display torque values from 5 to 100 ft-lbs. As you tighten a fastener, the needle on the dial will move and precisely display the amount of torque being applied at any given moment.
Digital wrenches work similarly, but show the real-time torque value on an digital display.
This allows for very precise torque measurements, usually accurate to within +/- 2% on high-quality dial and digital wrenches.
Click-Type Torque Wrenches
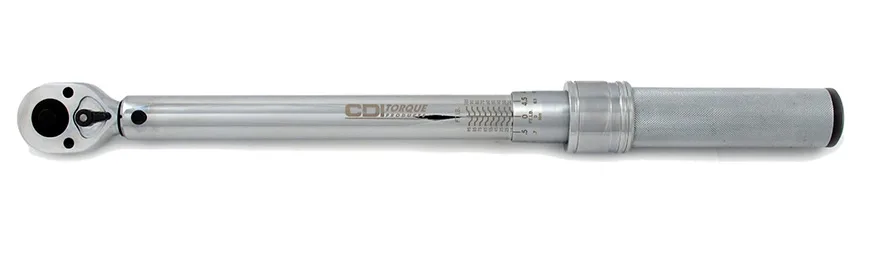
Click-type torque wrenches don’t have a measurement scale. You set the desired torque beforehand using a calibration handle.
When the set torque value is reached, the wrench will make a distinct “click” sound.
This signals that the target torque has been reached and you should stop tightening the fastener.
Since click wrenches don’t have a scale, you need to rely on the calibration and the audible click for accuracy.
Quality click torque wrenches are calibrated to be accurate to +/- 4% or better.
Understanding how to read the different measurement scales is a key skill for using any torque wrench correctly.
Always double-check the units marked on the scale and make sure you are applying the proper torque value for the application.
Setting the Desired Torque
Setting the torque wrench to the proper torque setting is crucial for safe and accurate use.
Here are the steps to set the desired torque:
- Consult your vehicle’s service manual or the specifications from the part manufacturer to determine the correct torque value for the fastener you’ll be tightening. Improperly torqued fasteners can fail or damage parts.
- Locate the scale on the handle of the click-type torque wrench. This is typically engraved or printed on the handle.
- If your wrench has a range of torque settings, find the setting knob, switch, or adjuster. This allows you to select the needed torque range.
- Once you’ve identified the correct torque value and range, rotate the grip of the handle or turn the adjustment knob until the indicator points to the desired torque setting on the scale.
- For dial-type torque wrenches, rotate the dial until the needle points to the specified torque value.
- Double-check that the wrench is now properly set to the required torque. Refer to the service manual as needed.
- Some wrenches may require you to pull out on the head to lock in the setting before use. Consult the operating instructions.
- Setting the torque wrench precisely before use helps ensure you apply the appropriate amount of torque to the fastener.
Applying Torque to a Fastener
Proper technique and form when using the torque wrench is critical to get accurate torque readings and avoid injury.
Here are some key tips:
- Stand with proper footing and balance. You don’t want to be off-balance when exerting force on the wrench. Keep your feet about shoulder width apart and adopt an athletic stance.
- Maintain good ergonomic form. Hold the handle near the end to get better leverage. Keep your back straight, engage your core, and avoid twisting.
- Pull in a smooth, steady motion without jerking. Jerky or rapid movements can cause inaccurate torque readings.
- Pull at a 90 degree angle from the axis of the fastener. Pulling at an angle loses some of the force you generate.
- Use your dominant hand on the handle and your non-dominant hand to brace the head of the wrench. This gives you maximum control.
- Pull until you hear the click that indicates you’ve reached the preset torque. Do not over-tighten past the click.
- Allow the wrench to reset completely before repeating for the next fastener.
- Take breaks as needed if you are tightening many fasteners to avoid fatigue. Fatigue can lead to poor form and injury.
Proper technique protects you from injury and ensures you apply the right amount of torque to the fastener.
It’s not just about brute strength – good form allows you to work efficiently.
With practice, using a torque wrench properly will become second nature.
Maintaining and Calibrating
Proper maintenance and calibration are crucial for ensuring your torque wrench continues to provide accurate readings.
Here are some tips on caring for and calibrating your torque wrench:
- Store properly when not in use. Torque wrenches are precision instruments and should be handled with care. When not using your torque wrench, store it in a protective case away from moisture, dramatic temperature swings, and potential impacts. Never leave a preset torque wrench set at a high torque setting, as this can damage the internal spring mechanism over time.
- Keep clean. Make sure to keep your torque wrench free of dirt, grime, and other contaminants which could lead to inaccuracies or malfunctions. Wipe down after each use.
- Avoid drops. Dropping your torque wrench can knock it out of calibration, so handle with care. If you suspect your wrench may be inaccurate after a drop, discontinue use and have it recalibrated.
- Lubricate moving parts. Make sure to periodically lubricate the moving parts of your click-type torque wrench according to manufacturer specifications. This ensures smooth operation.
- Get recalibrated annually. Most manufacturers recommend having your torque wrench recalibrated at least once per year to maintain accuracy. Calibration services are offered by many tool companies or can be done in-house if you have the proper calibration equipment.
- Follow manufacturer instructions. Always adhere to the maintenance guidelines in your torque wrench’s manual to keep it performing optimally. Proper care will maximize your wrench’s longevity and precision.
Keeping your torque wrench properly maintained through regular calibration, cleaning, lubrication, and careful handling will help ensure you are consistently achieving your target torque values.
Follow manufacturer recommendations closely. An inaccurate torque wrench defeats the purpose of using this precision tool.
Safety Tips
Using a torque wrench properly is important for safety. Here are some key tips:
- Always double check that you have the torque wrench set to the correct torque setting for the fastener you are working on. Applying too much torque can damage the fastener and device. Too little torque can result in a loose connection.
- Ensure nothing is obstructing the handle or lever arm from moving freely and completely through its range of motion. Any obstructions could cause inaccurate torque readings.
- Keep your hands, clothing, jewelry and other body parts clear of the torque wrench and fastener as you apply torque. The wrench handle will quickly spin as force is applied.
- Use caution if needing to apply torque from an awkward position or angle. Make sure you have a stable stance and solid grip before applying pressure.
- Store the torque wrench carefully when not in use to avoid damage. Dropping or knocking the wrench can knock it out of calibration.
- Do not use torque wrench extensions or cheater bars for added leverage. This alters the calibrated settings. Only apply force directly through the wrench’s handle.
- Maintain and calibrate the torque wrench regularly according to manufacturer specifications. Using an out-of-calibration wrench can be unsafe.
- Never loosen a fastener with a torque wrench, only tighten. Loosening can damage the internal calibration mechanism.
- Select the right torque wrench for the application. Using the wrong type of wrench on certain fasteners is unsafe.
Following proper safety practices when using a torque wrench reduces the chance of injuries or damage. Take the time to use the right torque tool correctly.
Conclusion
Using a torque wrench properly is vital for achieving accurate and repeatable tightening results. To summarize, the key steps are:
- Select the appropriate torque wrench for your application based on the range of torque needed. Go with a click style wrench for more precision.
- Understand how to read the torque measurement markings or scale on your wrench. Always double check you have the right units.
- Set the torque wrench to your target torque setting before use. Refer to manufacturer specs when available.
- Make sure the fastener and wrench engage squarely when applying torque. Avoid over-tightening.
- Maintain your torque wrench with calibration and storage per the manufacturer’s recommendations.
- Follow basic safety rules like avoiding drops, ensuring good gripping conditions, and keeping body parts clear while applying torque.
Properly utilizing a torque wrench as described in this guide will lead to fasteners tightened to the right tension.
This prevents costly and dangerous overtightening or undertightening.
Take the time to learn the ins and outs of your torque wrench.
With practice and adhering to good torque techniques, you can feel confident your critical applications are assembled to specifications.